Is your current company that moves your goods not working well enough? Are you always facing delays, mistakes, and extra costs you didn’t expect? If your logistics partner is causing more problems than solutions, it may be time to find a new one.
Having the right company to move your goods can make or break how well your business does. Don’t settle for poor service from a company that is holding you back. There are many good and modern new logistics partners out there that can help make your operations run smoother, save you money, and give you an advantage over others.
Keep reading to learn about 7 good reasons why you should start looking for a new logistics company to move your goods.
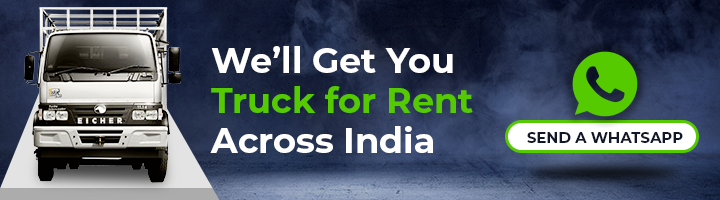
- Lack of Innovation
The logistics industry is quickly changing with new technologies like real-time tracking, automation, and analyzing data. If your current company is still using old methods and doesn’t want to modernize, it’s a big warning sign. A new innovative logistics partner will use cutting-edge solutions to make your supply chain operations better at every step. From using artificial intelligence to plan the most efficient routes, to automated warehouse systems that reduce human mistakes, to blockchain for new age tracking – a forward-thinking company uses the latest technology and tools to save you time and money.
- Hidden Fees and Lack of Transparency
Unexpected fees and extra charges that aren’t properly disclosed can quickly eat into your profits and make budgeting a nightmare. A trustworthy, ethical new logistics company will be completely clear about pricing from the very beginning. If your current company doesn’t explain pricing, be careful! Immediately ask for a clear, detailed breakdown of all costs including base rates, fuel extra charges, additional fees, and any other potential extra expenses. Being clear about costs is crucial for accurately planning and forecasting your logistics expenses.
- Recurring Mistakes and Errors
Mistakes like mishandled shipments, incorrect documentation, failed pickup attempts, and missed deadlines occasionally happen even to the best logistics providers. But if they become a frequent, unresolved issue with your current partner, it’s simply unacceptable. Even small, isolated errors can have a compounding domino effect leading to significant shipment delays, stockouts, angry customers, and loss of revenues. Look out for new logistics providers with robust processes, new age logistics tracking, workforce training programs, and integrated technology checks to prevent errors and minimize disruptions.
- Lackluster Technology and Outdated Systems
In today’s digital age, having access to modern, advanced technology is crucial for safe, efficient, and cost-effective new age logistics tracking operations. If your current provider still relies heavily on outdated legacy systems, it’s likely causing unnecessary delays, lack of real-time visibility, and higher operating costs. The new logistics tracking Cloud-based transportation management systems, automation for paperless workflows, and machine learning for intelligent load optimization are must-have technological capabilities that allow for seamless, data-driven operations that create tangible value.
- Subpar Customer Service
When shipment issues, exceptions, or delays crop up, you need a new logistics supplier that is quickly responsive, communicative, and able to take swift corrective action. If your current provider is unresponsive, brushes you off, lacks logistics expertise, or can’t seem to resolve issues satisfactorily, this lapse in customer service leads to frustration, extended disruptions, and loss of time and money. A top logistics company should offer robust support channels, and a dedicated account team, and develop issue escalation protocols to minimize impacts and get your shipments back on track promptly.
- Lack of Specialization
While some logistics providers cast a wide, generalist net, different industries have unique nuanced needs when it comes to specialized equipment, packaging, delivery timeframes, compliance requirements, and more. Using a jack-of-all-trades provider that lacks expertise and dedicatedly trained staff in your specific vertical can lead to errors, inefficiencies, and failure to capitalize on customized optimization opportunities. Whether you’re in the highly regulated pharmaceutical industry, the ambient food supply chain, or industrial project logistics, find a new logistics supplier that has extensive experience and skills for your niche.
- Missed Environmental Goals
More and more businesses are rightly prioritizing sustainability initiatives by reducing carbon footprints, minimizing environmental impact, and going green. If your logistics provider stubbornly clings to outdated practices that are anything but eco-friendly – like inefficient routing resulting in wasted fuel, excessive packaging waste, and prioritizing excessive cost-cutting over the environment – it could be severely hindering your ability to meet environmental, social, and governance goals. An environmentally conscious logistics partner with a sincere sustainability vision is non-negotiable. Look for one utilizing eco-friendly fleets, sustainable facilities, optimized load consolidation, recycled packaging, and more.
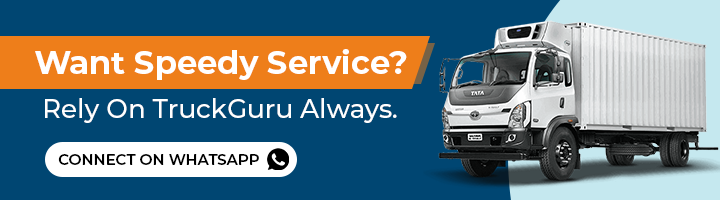
Conclusion
Choosing the right logistics partner is crucial for supply chain success and overall business growth. Don’t ignore the red flags or continue tolerating subpar service – a provider that is ill-equipped to meet your needs can directly lead to costly mistakes, missed opportunities, operational inefficiencies, and will not be able to cope up with the competition. Take the time to thoroughly evaluate your options and find a logistics company that is innovative, ethical, reliable, attentive, and aligns with your current and future business requirements. With the right logistics partner, you can streamline operations, save money, satisfy customers, and ultimately boost your profitability.